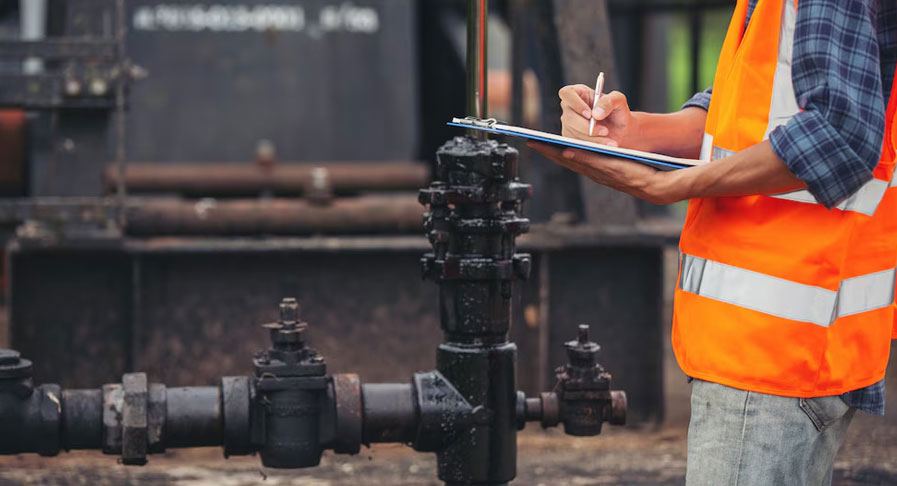
NDT Inspection
We at Reach Asset Care, our NDT technicians are highly skilled and qualified professionals with extensive training in advanced testing techniques. They possess a deep understanding of inspection methods and are proficient in detecting even the most subtle discontinuities in materials. They ensure thorough and accurate detection, providing reliable insights that guarantee the integrity and safety of the components.
Reach Asset Care uses these NDT methods to evaluate the condition of equipment and structures, detect defects or irregularities, and ensure adherence to industry standards and regulations. By employing these techniques, we deliver precise and dependable inspection results without damaging or disrupting the tested components.
Visual Examination
Visual Testing (VT) is a non-destructive testing (NDT) method that relies on the direct observation of a component to identify surface defects. As the most basic and widely used NDT technique, it often acts as a first step before employing more advanced testing methods. VT can be conducted using the naked eye or enhanced with optical tools such as magnifiers, borescopes, or video scope.
Magnetic Particle Inspection
Magnetic particle testing (MT) is a non-destructive testing (NDT) method employed to identify surface and near-surface flaws in ferromagnetic materials. In MT, the material is magnetized, and fine ferromagnetic particles are then applied to its surface. Any discontinuities, such as cracks or voids, disturb the magnetic field, generating a leakage field. These leakage fields attract the ferromagnetic particles, making the discontinuities visible.
Dye Penetrant Testing
Liquid Penetrant Testing (PT) is a non-destructive testing (NDT) method that utilizes specially formulated liquids to detect surface defects in solid and nonporous materials. The process involves applying a penetrant to the surface of the test object, allowing it to infiltrate any surface-breaking flaws. Afterward, a developer is applied to draw the penetrant out, creating a visible indication of the defect. This method is particularly effective for identifying surface cracks, seams, and other flaws that may not be visible without inspection.
Ultrasonic Thickness Testing
Ultrasonic testing (UT) is a non-destructive testing (NDT) method that utilizes high-frequency sound waves to identify and measure discontinuities in industrial components. Like naval sonar and medical ultrasound, UT in industry involves sending sound waves into a material and analysing the returning echoes to gather information about the internal structure of the part being tested.
The advantage of this method lies in its versatility, allowing it to be used in various industries and environments. A skilled NDT technician applies their expertise and experience to select the appropriate technique for each situation and conveys the results through various reporting formats.
Corrosion Mapping.
Corrosion presents a critical challenge across various industries, leading to significant economic losses and posing serious safety risks. In the oil and gas industry, pipelines, storage tanks, and other infrastructure are vulnerable to corrosion due to the corrosive nature of hydrocarbons, the presence of impurities, and electrochemical reactions. The marine and offshore sector faces heightened corrosion risks from constant saltwater exposure. Power generation facilities, including fossil fuel and nuclear plants, must manage corrosion caused by high temperatures, humidity, and corrosive byproducts. In aerospace, components are exposed to harsh conditions such as high altitudes, moisture, and temperature variations. Similarly, infrastructure like bridges and highways endures corrosion from environmental exposure and de-icing chemicals used in construction and maintenance.Corrosion mapping can be performed using zero-degree ultrasonic probes.
We at Reach Asset Care, our team of certified and highly skilled NDT Technicians specializes in delivering accurate and reliable corrosion mapping using industry-standard techniques. We utilize advanced Ultrasonic Testing (UT) equipment with zero-degree probes to perform systematic thickness measurements across Tanks, Vessels, Pipelines, and Plates, and other metallic structures that prone to corrosion.
By applying a structured grid layout, we generate detailed corrosion maps that highlight wall thinning and material degradation. This non-destructive method ensures thorough coverage without the need for insulation removal—only requiring a clean and accessible surface. External coatings can remain intact.
Our approach guarantees high-quality, dependable data that helps you make informed decisions about asset integrity—without interrupting operations or compromising safety.
Eddy Current Testing
We at Reach Asset Care, our NDT technicians are highly skilled and qualified professionals with extensive training in Eddy Current Testing. They possess a deep understanding of inspection methods and are proficient in detecting even the most subtle discontinuities in materials. They ensure thorough and accurate detection, providing reliable insights that guarantee the integrity and safety of the components.
Eddy Current Testing (ECT) is a highly effective and efficient non-destructive testing (NDT) method that relies on electromagnetic induction to detect and evaluate surface and near-surface flaws in conductive materials. By monitoring variations in the eddy currents, the testing equipment can accurately identify surface cracks and planar discontinuities—particularly in ferritic materials such as welds, heat-affected zones, and base metals.
We at Reach Asset Care, our NDT technicians are highly skilled and qualified professionals with extensive training in Eddy Current Testing. They possess a deep understanding of inspection methods and are proficient in detecting even the most subtle discontinuities in materials. They ensure thorough and accurate detection, providing reliable insights that guarantee the integrity and safety of the components.
Eddy Current Testing (ECT) is a highly effective and efficient non-destructive testing (NDT) method that relies on electromagnetic induction to detect and evaluate surface and near-surface flaws in conductive materials. By monitoring variations in the eddy currents, the testing equipment can accurately identify surface cracks and planar discontinuities—particularly in ferritic materials such as welds, heat-affected zones, and base metals.
Advantages of the ECT
Faster
Cost Effective
No need of paint removal on surface to be tested coating thickness
Where do we use it
Determine the Coating thickness of engineering components whether its metallic or non-metallic.
On weld overlay
On Residual Bond
Corroded wall thickness
At Crane inspection:
Unlock Cost Savings and Precision with Eddy Current Testing in the Crane Industry Eddy current testing offers significant advantages to crane owners and the crane industry by enabling the detection of surface flaws beneath protective coatings—without the need for costly paint removal and reapplication.